Al Barsha Precision Moulding Dies: Where Innovation Meets Artistry
Al Barsha Precision Moulding Dies. Ind. L.L.C (BPTUAE) is a world class mould making facility. The high performance injection moulds created by bpt blend Craftsmanship with Technology. They are products that combine innovation and artistry – they are products that we, as bpt UAE, are extremely proud of.
Facilities
We are able to manufacture moulds with mould bases up to 60″ x 24″ holding sizes within .0002″ and positions within .0005″.
Our machines are capable of manufacturing hardened tool steel components at 62+ Rockwell.
We are able to high speed machine sizes up to 22″ x 14″ x 10″ to extremely tight tolerances, holding size and position within .0002″.
Many of our machines are equipped with pallet changers and/or 3R multi station work holding systems. This enables us to run our machines unattended. We also have extensive grinding capabilities which include:
- Jig Grinding
- Surface/Wet Grinding parts up to 46″ x 58″ flat and parallel within .0002″
- CNC O.D./I.D Grinding parts up to 12″ in dia. (O.D.) and 24″ long
Actions
- Hydraulic Core Pull
- Hydraulic and Mechanical Unscrewing
- Collapsible Cores
- Mechanical Slides
- Lift Mechanisms
- Lift & Twist Mechanisms (for undercut release)
- In-mould Closing
- In-mould Labeling
- Flip-Tops
Capacities
- Plate Machining: 36″ wide x 48″ long
- Mould Handling Weight: Crane capacity to 2000 kgs.
- Average moulds under construction: 15
- Annual mould Production: 75 ~ 100 moulds
- Normal Design and Build Delivery Time: 4 – 5 weeks.
Tolerances
- Plates and misc. mouldbase Components: ± .0005 in. (± .012 mm)
- Cavity Stack Components: ± .0002 in. (± .005 mm)
- Laminated Inserts: ± .0001 in. (± .0025 mm) or closer
Mould Types
- Multi-Cavity
- Valve Gate
- Hot Edge
- 90 deg. Hot Melt
- Horizontal Valve Gate
- 2 Material
- Hot Runner
- Hot-to-Cold Runner
- 3-Plate
- Stripper Plate
- Stack
- 2-Color
- LSR moulds
- Two Material
- Cold Deck or Cold Runner
- Cold to Hot Runner
- Fully Automated De-moulding
- Automation of Secondary Operations
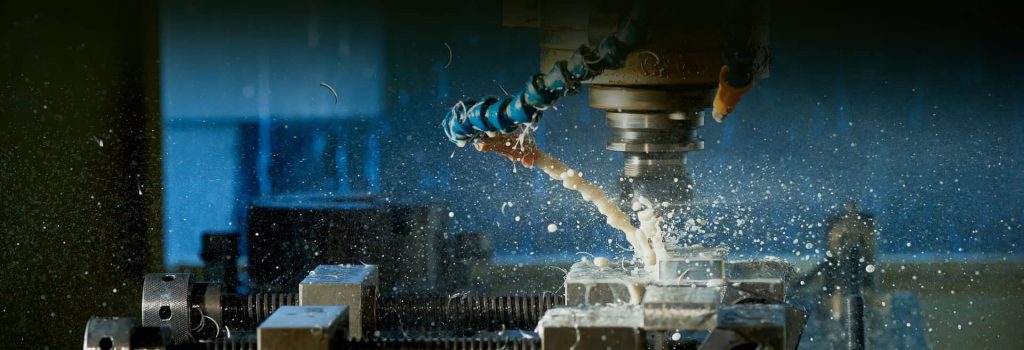
The implementation of advanced machining and manufacturing techniques allows BPTUAE to produce all mould components in the shortest time. Efficient processes don’t just save time; they also save money.
Our design and mould making team can create your ideas and enhance it into a 3D cad file using different modelling softwares. bpt UAE then design the mould and adjust for the type fo material as per clients specific application.
There after we use state of art software to machine the plates with high precision CNC milling to start building the mould.
Our highly skilled team can provide precision work andquality in said specific time span. Our mould making process used many materials like P20, D2, Gunmetal, Alumec, EN 8,EN 24, C 45, SS, MS, 2136, Aluminium, Brass, Copper and Carbon.
The machine shop is also equipped with CNC mills, EDM sinker, wire EDM, surface grinder, polising station and sand blaster. We take great pride in our work and aim to make your product work to your expectations. At Al Barsha Precision Moulding Dies. Ind. L.L.C, we build more than injection moulds and plastics, we build trust and mould relationships that you can count on.